High speed and high precision laser welded pipe production line
Product Description
Product Features
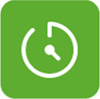
High power welding
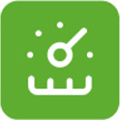
Up to 15 m/Min
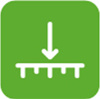
Weld deflection position accuracy ≤ 0.1mm
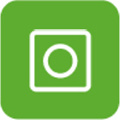
For> 800MPa grade high strength steel welding
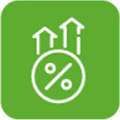
>96%
Process flow
The core barriers and difficulties of laser welding equipment mainly involve the following aspects
welding quality control
The consistency, aesthetics and mechanical properties of the weld quality must meet strict standards. This includes avoiding porosity, cracks, incomplete penetration, burn-through and weld distortion.
Technical complexity of equipment
Laser welding equipment needs to integrate feeding equipment, edge milling equipment, welded pipe forming equipment, laser equipment, cut-off equipment, online eddy current testing equipment, robot automatic feeding equipment and other precision mechanical, electronic, optical, material science and other multidisciplinary technologies to ensure accurate control of the welding process.
control system stability
In order to improve welding efficiency and quality, welding equipment needs to integrate advanced automation and intelligent solutions.
automation and intelligent level
The equipment control system must be able to adjust the welding parameters accurately and in real time to adapt to different welding environments and requirements.
Material adaptability
The welding equipment should be able to adapt to a wide range of materials and different diameter thicknesses, especially when dealing with ultra-high strength steel greater than 800Mpa.
Maintenance and stability of equipment
High-performance welding equipment needs to be highly reliable and easy to maintain, reducing production downtime.
Introduction of Integrated Advanced Control Technology to Overcome the Core Barriers and Difficulties of Laser Welding Equipment
High precision power drive control technology
Use high-precision 15 servo power drive control, adaptive control and real-time feedback system to ensure stable welding speed.
Using machine vision and sensing technology
We use the machine vision inspection and sensing technology of Cognex Technology Company in the United States to realize the monitoring of weld deflection, real-time monitoring of welding quality and automatic defect detection. Integrated development of our automated and intelligent welding inspection monitoring software.
Integrated research and development of multiple technologies to achieve new laser welding technology
In order to improve welding efficiency and quality, welding equipment needs to integrate advanced automation and intelligent solutions.
Focus on the development of high-strength steel pipe high-speed (15 meters), high-power (ten thousand watts) laser welding process and forming mechanism, lightweight component structure simulation design and service performance evaluation, breakthrough laser weld tracking, high-speed precision centering equipment and process, laser welding defect control, laser welding forming precision control and other key technologies, developed a fully automated high-strength steel laser welding pipe equipment production line and laser welding process.
• Integrated real-time monitoring system:
The welding speed is monitored and adjusted in real time by sensors and feedback system to keep it within the set range.
• Determination of optimal parameters by pre-test:
Multiple rounds of pre-tests were conducted to test different welding speeds to find the best speed and acceleration parameters.
Several rounds of iteration and optimization are performed to achieve stable and accurate welding speed control through R & D and debugging improvements.
Key words:
Related Products
Welcome your message consultation
*Leave your contact information to get a free product quote